Переработка отходов сельскохозяйственных
производств
Аппарат вихревого слоя
Особенности вихревого слоя умело используются при очистке сточных вод, содержащих тяжелые металлы, что позволяет резко сократить расход реагентов, добиться более полной очистки и перевести эти процессы на непрерывный режим.
Ферромагнитные частицы, которые находятся в рабочей зоне аппарата вихревого слоя, под воздействием электромагнитного поля совершают интенсивное перемешивание поступающих в реакционную зону реагентов.
Под воздействием удара и трения происходит их измельчение до коллоидной степени дисперсности. Образовавшийся коллоидный металл является хорошим восстановителем. Одновременно с образованием коллоидного металла в процессе диспергирования ферромагнитных частиц в вихревом слое идет образование водорода за счет электролиза воды.
Оба фактора существенно влияют на реакцию восстановления металлов в сточной воде. Эта способность вихревого слоя позволяет значительно сократить расход сернокислого железа на восстановление металлов и даже добиться полного восстановления металлов в сточной воде только за счет коллоидного металла и выделяющегося водорода.
Процесс восстановления длится доли секунды, что обеспечивает возможность непрерывного ведения процесса с большей скоростью.
Интенсивное перемешивание реагентов и воздействие электромагнитных полей, а также диспергирование образовавшихся соединений приводит к тому, что образовавшиеся гидроокиси металлов более дисперсны, чем полученные в аппаратах с механическими мешалками.
Увеличение дисперсности осадков не приводит к замедлению процесса их отстаивания.
Наоборот, осаждение частиц твердой фазы после реакции происходит в полтора-два раза быстрее, чем после реакции в аппарате с мешалкой. Сказывается интенсивная магнитная обработка образовавшейся суспензии, приводящая к изменению поверхностного натяжения на границе жидкость-твердое тело.
Важнейшей особенностью вихревого слоя является тот факт, что после обработки в нем изменяются физико-химические свойства вещества, что в большой степени влияет на химическую активность обрабатываемого продукта.
Применение аппарата с механическими перемешивающими устройствами требует больших производительных площадей и значительных капитальных затрат.
Длительность циклического прочеса очистки при использовании данного метода составляет от 30 до 120 минут.
В противоположность этому в комплект установки с применением аппарата для очистки сточных вод от металлов методом химического восстановителя в щелочной среде при одновременном осаждении металлов в виде гидроокисей входят лишь емкости для сернокислого железа и известкового молока с дозаторами, один аппарат и фильтр или шламонакопитель- отстойник.
Технология комплексной очистки илистых отложений прудов-накопителей от органических веществ
с помощью наноструктурированных катализаторов
Возрастающие масштабы производства свенины, мяса птицы и говядины способствовали выработке значительных объемов сточных вод, содержащих соли, токсичные и нетоксичные органические примеси. На территории страны появилось колоссальное количество прудов-накопителей стоков, в которых в течение десятков лет сформировывался многометровый слой ила.
К настоящему моменту эти пруды накопители усугубляют неблагоприятную экологическую ситуацию, в связи с чем остро стоит вопрос утилизации содержащихся в них отходов с минимальным ущербом для окружающей среды.
Существующие пути решения данной проблемы:
-
технология «Лессорб» предполагает смешивание шлама пруда-накопителя с известью. При этом органические загрязнители, представляющие большую опасность для природы, не разрушаются. Для реализации этой технологии требуется много месяцев. Экономические затраты на 1 пруд объемом примерно 70000 м3 составляют не менее 20 млн. рублей;
-
технология термического разложения отходов не менее опасна, требуется изготовление специального дорогостоящего оборудования, время обработки – 3-5 лет, затраты на один пруд – 60-80 млн. рублей.
Первый способ не является радикальным, хотя он и не такой затратный. Второй – позволяет полностью избавиться от вредных органических загрязнителей, но высокая стоимость технологии делает ее практически неприменимой.
В мировой практике не существует радикального экономичного способа утилизации прудов-накопителей предприятий органического синтеза.
Технология диструкции иловых отложений
Разработан представляемый метод утилизации органических соединений илистых отложений, основанный на каталитическом окислительном разложении органических соединений по схеме:
CxHy CO2 + H2O.
В качестве катализаторов окислительного синтеза используются ультрадисперсные системы, а именно наноструктурированные металлы и оксиды металлов I, VI и VIII групп периодической системы Д.И. Менделеева. Проведенные натурные испытания метода показали его высокую эффективность.
Соотношение высоты ила и поверхностных вод составляла 11:3.
Ввод композиции наноструктурированных материалов осуществлялся в плотный слой ила из расчета по 0,01 г ультрадисперсной суспензии на 1 м3 ила.
Процесс окислительной деструкции органических соединений в присутствии наноструктурированных материалов протекал в течение 60 дней.
Илистые отложения анализировались на сухой и прокаленный остатки (%), содержание органических веществ (%), ХПК (мг О2/мг) до начала процесса диструкции и через 6, 27, 48 и 60 суток после обработки.
За 60 суток содержание органических веществ в иле сократилось на 96,4 %.
По окончании процесса окислительной деструкции усредненная проба илового осадка из пруда-накопителя была направлена в Центр лабораторного анализа и технических измерений по Центральному Федеральному округу на биотестирование. Его результаты показали, что полученный после обработки отход может быть отнесен к IV классу опасности (низкая степень вредного воздействия на окружающую природную среду).
До обработки иловый осадок относился к 3 классу опасности.
Подтверждение возможности проведения низкотемпературного окислительного синтеза органических соединений в присутствии ультрадисперсных систем (наноструктурированных металлов и оксидов металлов I, VI и VIII групп периодической системы) позволило разработать и применить технологию утилизации прудов-накопителей, содержащих преимущественно органические соединения.
Разработанная технология состоит из следующих этапов:
I этап. - Утилизация органических соединений пруда методом обработки ультрадисперсной системой №1 (удаление основной массы органических соединений).
II этап. - Углубленное удаление органических соединений пруда-отстойника методом обработки ультрадисперсной системой №2 (удаление остаточного количества органических соединений).
III этап. - Сжигание части остаточного количества органических соединений с помощью пиролизной печи и выработки электрической и тепловой энергии для внутренних нужд производства (обеспечение полной автономности переработки), а также продажи излишков энергии в качестве товарного продукта
Второй этап утилизации органических соединений состоял из введения ультрадисперсной суспензии (приготовленной в соответствии с таблицей 2) в плотный слой илистых отложений пруда-отстойника посредством распыления суспензии над зеркалом пруда-отстойника из расчета 0,000162 м3 ультрадисперсной суспензии на 1 м3 ила.
Реализация второго этапа утилизации органических соединений обеспечила снижение количества органических соединений до концентраций обеспечивающих IV класс опасности.
Затраты на материалы для этапов обработки, обеспечивающих достижение IV класса опасности были в 10 раз меньше, чем технология утилизации илистого отложения смешением шлама пруда-накопителя с известью.
Разработанная технология низкотемпературного окислительного синтеза органических соединений в присутствии ультрадисперсных систем была также реализована в сентябре 2008 г. для пруда-накопителя, содержащего формальдегид, нитро и аминосоединения, фенолы, неорганические кислоты, нефтепродукты, соли и соли тяжелых металлов.
Реализация уже первого этапа разработанной технологии обработки позволила за 29 суток процесса окислительной деструкции достичь снижения содержания органических веществ до уровня, обеспечивающего класс опасности близкий к IV.
В результате процесса деструкции илистых отложений формируются органические удобрения для сельского хозяйства.
Так в пруду объемом 68 000 м3 после обработки по предлагаемой технологии было сформировано около 30 000 м3 органических удобрений.
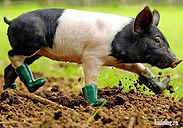

