Переработка отходов сельскохозяйственных
производств
Состав жидкой фазы представляет собой фракцию углеводородов с температурой кипения от 200 – 440оС. Известно, что углеводороды с температурой кипения до 400оС (С12 – С22) используются в качестве дизельного или котельного топлива. Теплотворная способность топлива, содержащего углеводороды с температурой кипения 200-400оС, составляет 35-40 кдж/г [2, 9]. Расчеты показали, что энергетического потенциала образующегося конденсата достаточно для предварительной сушки ИАИ до остаточной влажности 10%, что приведет к значительному снижению затрат на его термическую утилизацию.
Газообразные неконденсируемые продукты пиролиза имеют следующий состав (%):
СН4 40,0-45,0
С2Н6 20,0 – 23,0
Н2 20,0 -22,0
С2Н4 6,0 -8,0
СО 3,0 – 5,0
СО2 7,0 – 8,5
N2 4,0-6,0
H2S 2,5-4,0
и представляют собой среднекалорийное топливо. Такой газ можно также использовать в самом процессе пиролиза для поддержания температуры и для сушки исходного сырья. Теплотворная способность повышается, если использовать горячий газ. Горячие неконденсируемые газы пиролиза имеют теплотворную способность – 44000 кДж/кг.
Вторично используемые пиролизные газы перед выбросом в атмосферу должны подвергаться очистке от оксидов серы, например, абсорбционными методами с использованием в качестве абсорбента раствора оксида кальция.
При пиролизе ИАИ образуется органоминеральная композиция – крупно-дисперсный материал черного цвета, содержащий пироуглерод. Основу минеральной части композиции составляют оксиды алюминия и кремния (22% и 25% соответственно).
Переработка активного ила
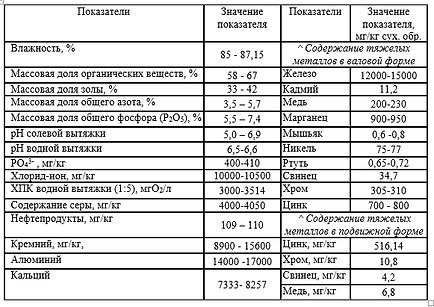





Пиролиз активного ила
Переработка различных органических отходов человеческой жизнедеятельности методом пиролиза является перспективной сферой, потому что при переработке отходов таким методом количество канцерогенных и загрязняющих факторов, выделяемых в окружающую среду в процессе переработки этих отходов должно быть значительно меньше количества таких же факторов, выделяемых отходами в процессе естественного распада. Кроме того, в результате переработки отходов методом пиролиза получается ценные высоколиквидные продукты — вторичное углеводородное сырье и топливо, значение которых в настоящее время все более возрастает в связи с истощением природных источников такого сырья.
Пиролиз — термическая деструкция исходного вещества (разрушение нормальной структуры вещества посредством высокой температуры, с ограниченным доступом кислорода).
Быстрый пиролиз (БП) — пиролиз, при котором подвод тепловой энергии к исходному веществу производится с высокой скоростью и без доступа кислорода (либо воздушной смеси в которой присутствует кислород).
Если медленный пиролиз подобен (условно) процессу доведения воды до состояния закипания, то БП условно подобен процессу попадания капли воды в раскаленное масло («взрывное вскипание»).
Отличительными особенностями БП являются:
— способность построения непрерывного замкнутого технологического производственного процесса;
— минимальное содержание угарного газа, при практическом отсутствии углекислого газа;
— относительная «чистота» выходных продуктов пиролиза, из-за отсутствия процесса бертинирования («осмоления»);
— минимальная энергоемкость процесса, по сравнению с другими видами пиролиза;
— процесс сопровождается выделением тепловой энергии (экзотермические реакции превосходят эндотермические);
— управляемость температурными режимами процесса, с возможностью (при определенных условиях) построения «управляемого синтеза углеводородов» и т.д.
Однако, БП требует тщательной подготовки исходного сырья:
— измельчения до как можно меньшего эквивалентного диаметра частиц исходного вещества;
— сушку исходного вещества (эндотермия) до как можно меньшей относительной влажности (идеально до 0 % — абсолютно сухое вещество).
Если нивелировать эти недостатки (каким либо образом), то себестоимость выходных продуктов БП становится значительно ниже традиционных, полученных из: угля, нефти и природного газа.
Получены продукты переработки активного ила:
1. Синтетическая нефть (представляющая собой подобие природной нефти) -предназначена либо для дальнейшей переработки на установках органического синтеза в моторные топлива, либо для использования в системах ТЭЦ и котельных, вместо традиционных, полученных из сырой нефти;
2. Твердое углистое вещество (ТУВ) — высокоуглеродистый материал (ВУМ), представляющий собой порошкообразный кокс (полукокс) — предназначен для использования в металлургической, химической, пищевой и шинной отраслях промышленности, в системах ЖКХ и энергетики (как высококалорийное топливо);
3. Синтез-газ, представляющий собой очищенную и осушенную газовую смесь (метан, пропан, водород и т.д. со следами СО) — предназначен для использования в энергетических системах и системах потребления газа;
4. Тепловая энергия (высвобождаемая в процессе быстрого пиролиза) — предназначена для использования в системах ЖКХ и АПК, а также в целях генерации электроэнергии.
Внешний вид стационарных пиролизных установок, выпускаемых промышленностью РФ
Использование активного ила в качестве удобрения сельскохозяйственных культур в условиях загрязнения территории может позволить решить сразу несколько эколого-агрохимических проблем за счет их взаимодействующего синергизма: утилизация активного ила, повышению устойчивости культур и плодородие почв, снижение содержания радиоцезия в продуктах растениеводства.
Однако, при использовании активного ила следует строго соблюдать принцип: соответствие активного ила СаНПиН 2.1.7.573-96; ГОСТ Р17.4.3.07-2001 и Типовому технологическому регламенту использования ОСВ в качестве органического удобрения.
Технология переработки активного ила включает
1. при необходимости - удаление излишней влаги на центрифуге или деканторе
2. обеззараживание отжатой воды до требований сброса в водоемы РХН
3. сушку твердой фракции ила до 10% влажности
4. обеззараживание и дезактивация сухого ила
5. при необходимости - обогащение биологическими присадками
6. при необходимости - гранулирование
7. фасовку в тару
В итоге получаем товарную продукцию - органические удобрения
Хим. состав А.и. обусловлен составом клеточного в-ва микроорганизмов. Сухое в-во А.и. состоит из органической (беззольной) части и золы и представляет собой примеси, присутствовавшие в исходной сточной воде и трансформированные в биомассу, а также в-ва, адсорбированные хлопьями А.и.
Элементный состав беззольной части А.и. (как и состав клеточного в-ua) определяется осн. органогенами: углеродом, кислородом, водородом, азотом.
Соотношение этих элементов в беззольном в-ве А.и. зависит от состава обрабатываемых сточных вод, технологии, режима очистки и может существенно изменяться.
В среднем на долю углерода приходится 50— 52%, кислорода 29—33%, водорода б— 8%, азота 8—12%, беззольного в-ва А.и.
Соотношение элементов в А.и. определено в 1952 и представлено в виде "формулы" клеточного в-ва C5P7NO2. Эта формула используется для всех расчетов, связанных с кинетикой биохимич. процессов очистки воды и синтезом клеточного в-ва, точность ее для практич. целей оказывается достаточной, Значение удельной ХПК А.и. ста-ким соотношением осн. органогенов составляет 1,42 мг/мг.
Примерно 75—80% беззольного в-ва А.и. приходится на долю белков, жиров и углеводов, остальные 20—25% составляет негидролизуемый остаток.
Более всего в активном иле белков, содержание к-рых колеблется в среднем от 40 до 60% (в расчете на безвольное в-во). Кол-во белков в А.и. не постоянно и зависит от его видового состава и возраста.
Углеводы составляют 3—20%, жиры 10—30%.
Зольность А.и. колеблется в очень широких пределах — от 10 до 40%, для А.и. городских очистных станций она обычно составляет 25—30%. В зольной части А.и. обнаруживаются все элементы, присущие клеткам организмов (Р, S, К, Na, Ca, Mg, Fe и т.д.). Однако в А.и. по сравнению с клеточным в-вом значительно возрастает содержание железа и кремния.
При биологч. очистке жесткой воды в хлопке А.и. обнаруживается нерастворимый фосфат кальция, увеличивающий плотность хлопьев
Активный ил состоит из живых организмов и твердого субстрата.
Живые организмы представлены бактериями, одноклеточными животными, червями (коловратки, отряд немотод), плесневыми грибами, дрожжами, акцемиляцетами. И реже насекомыми (в виде личинок), рачками, клещами, а также водорослями. Все эти организмы образуют биоценоз.
Низкий трофический уровень бактерии и водоросли. Бактерии образуют скопление окруженными слизистым слоем (капсулы), такие скопления называют зооглея. Слизистые вещества содержат антибиотики, которые подавляют рост нитчатых бактерий. Нитчатые бактерии не имеют слизистого слоя и с меньшей скоростью окисляют загрязнение, с точки зрения физической химии активный ил представляет собой коллоидную систему, (все растворы делятся на две части: истинные и коллоидные).
Часто встречающиеся виды микроорганизмов в составе активного ила:
-
коловратка нотоммата
-
зооглея «оленьи рога»
-
аспидиска (брюхоресничная)
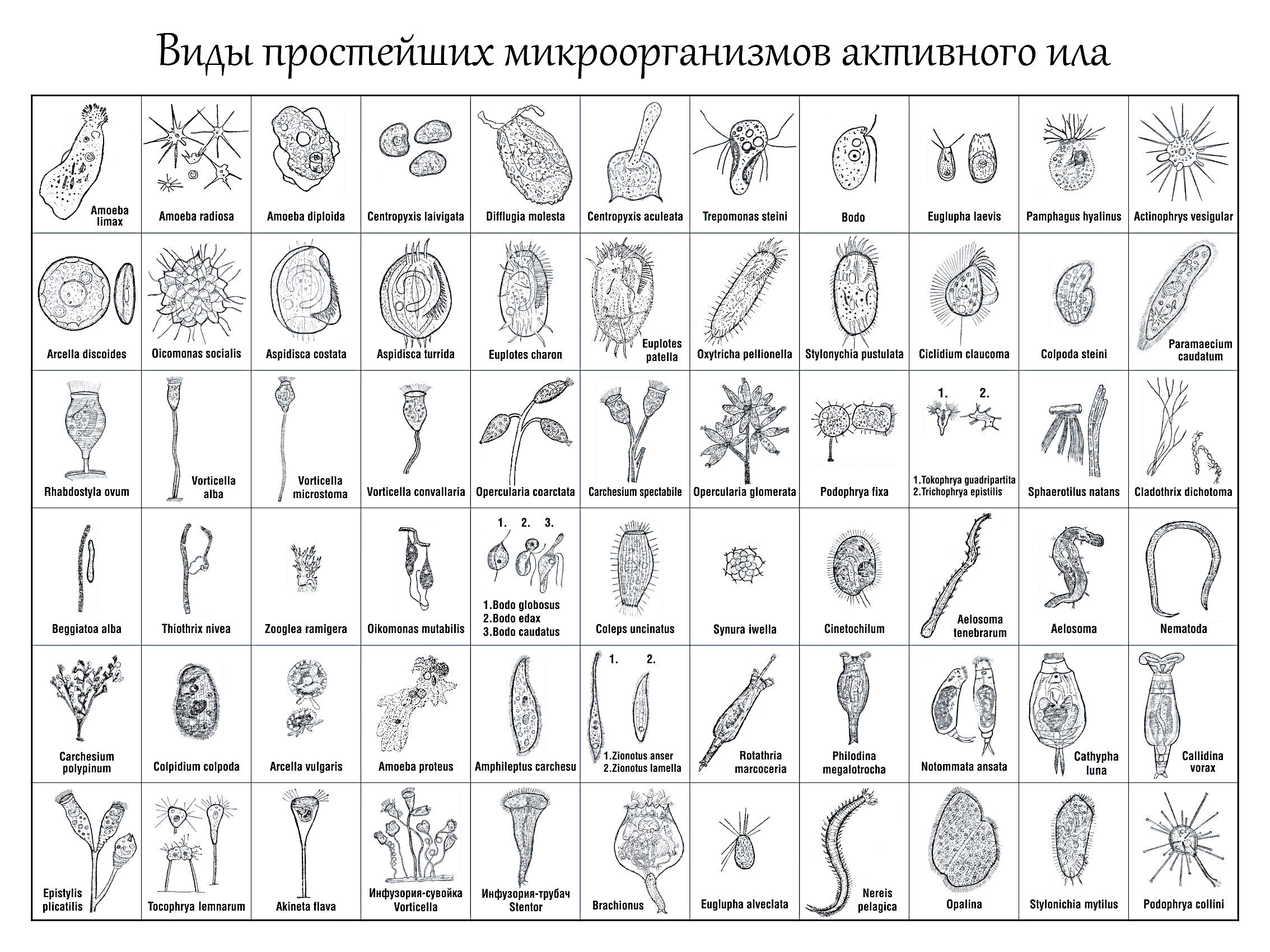
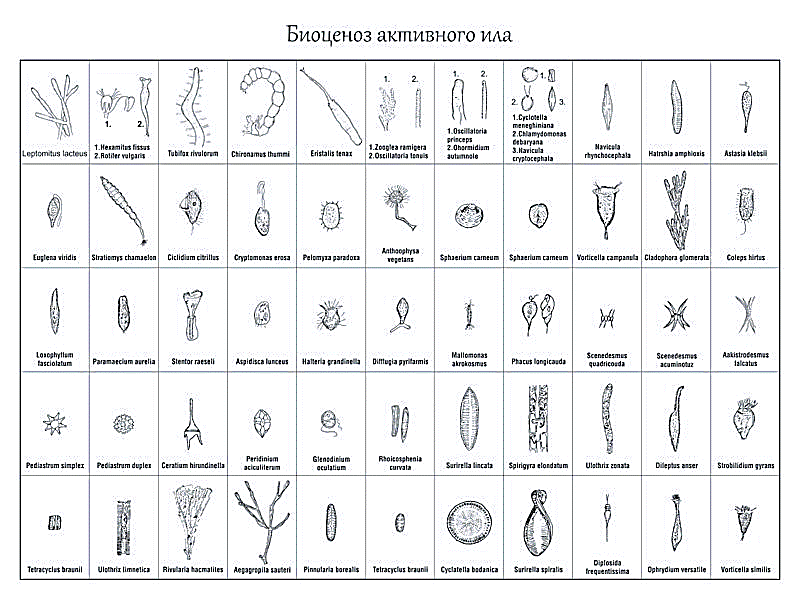
Продукты переработки активного ила
Из Аи можно получать следующие продукты:
-
биоудобрения;
-
корм для скота, птицы, рыбы, зверей и т.д.
-
синтетические энергоносители (синтетическая нефть, газ, углерод);
-
композитные жидкие энергоносители (аналог печного топлива).
Биоудобрения.
Экологически безопасные, высокоэффективные.
Технология производства заключается в сепарации исходного продукта от инородных включений, внесении активных ингредиентов, сушке и гранулировании полученного удобрения.
Рецептура удобрений корректируется с помощью Всероссийского научно-исследовательского института органических удобрений и торфа (ФГБНУ ВНИИОУ).
Из 100 тонн отходов 50% влажности можно получить до 50 тонн удобрения.
Корм для скота, птицы, рыбы, зверей и т.д.
Экологически безопасный, с высокой усвояемостью.
Технология производства заключается в сепарации исходного продукта от инородных включений, промывке водой исходной массы, сепарации крупных фракций непереваренного корма, внесении ингредиентов, улучшающих питательность корма, сушке и гранулировании полученного корма.
Из 100 тонн продукта 50% влажности можно получить до 30 - 50 тонн корма.
Энергоносители.
Газообразные, жидкие и твердые - аналоги угля, нефти и природного газа.
Технология производства заключается в сепарации исходного продукта от инородных включений, пиролизе продукта для получения синтетической нефти, газа и золы.
Нефть можно использовать в качестве котельного топлива, но можно произвести ее дальнейшую возгонку для получения бензина, керосина и дизельного топлива. Газ используется для внутренних технологических нужд. Зола используется в качестве удобрения.
Из 100 тонн исходного продукта 50% влажности можно получить до 30 - 40 тонн энергоносителей
Композитные жидкие энергоносители
Топливная жидкая композиция - смесь мелкодисперсного продукта и твердого или жидкого топлива (угольный отсев, отработанное автомобильное, трансформаторное или растительное масло). Топливная композиция – аналог печного топлива.
Получение топливной композиции осуществляют следующим образом:
Производится сепарация исходного продута от инородных включений, затем его измельчение до среднего размера частиц 300-500 мкм.
Твердое топливо (угольный отсев) предварительно измельчают до размера частиц не более 3 мм.
Затем смешивается измельченный продукт и твердое топливо (или добавляется жидкое минеральное масло) в пропорции 3:1.
Полученную смесь доводят до 70-75% влажности и производят диспергирование, смешение и гомогенизацию.
Из 100 тонн продукта 50% влажности и 20 тонн угольного отсева можно получить до 90 - 100 тонн топлива.
Использование активного ила в качестве корма для скота
Эта тема хорошо разработана и активный ил широко применяется в откорме скота.
Технология переработки активного ила включает
1. при необходимости - удаление излишней влаги на сепараторе
2. обеззараживание отжатой воды до требований сброса в водоемы РХН
3. сушку твердой фракции ила до 10% влажности
4. обеззараживание и дезактивация сухого ила
5. при необходимости - обогащение биологическими присадками
6. при необходимости - гранулирование
7. фасовку в тару
В итоге получаем товарную продукцию - кормовую добавку
Получаемая при пиролизе синтетическая нефть.
Полученная при пиролизе синтетическая нефть с помощью микро-НПЗ подвергается разгонке на три фракции – бензин, керосин и дизельное топливо. Полученное топливо предлагается используется для питания автомобилей хозяйства и дизельных электростанций
Микро-НПЗ
Микро-НПЗ предназначена для переработки пиролизной жидкости в ГСМ и получение на выходе светлых нефтепродуктов при самых минимальных размерах НПЗ.
При этом обеспечивается надежность эксплуатации при минимальной стоимости комплектующих, не требовательна к сырью.
Установка непрерывного действия, контроль процесса автоматический.
На выходе 3 нефтепродукта: бензин, керосин и дизельное топливо.
Это деление условное.
В основу Микро-НПЗ заложены главные принципы:
- качество получаемых нефтепродуктов;
- безопасность эксплуатации в соответствии со всеми нормами промышленной безопасности;
- надежная работа в режиме эксплуатации;
- простота в эксплуатации оборудования.
Состав микро НПЗ
1. Печь;
2. Испаритель;
3. Бак сырьевой;
4. Насос закачки сырья;
5. Насос подачи сырья в испаритель;
6. Насос орошения;
7. Воздушный калорифер охлаждения сырья;
8. Струйный скруббер;
9. Шкаф управления технологическим процессом;
10. Крекинг-реактор;
11. Воздушный калорифер охлаждения первой парогазовой фракции;
12. Воздушный калорифер охлаждения второй парогазовой фракции;
13. Воздушный калорифер охлаждения крекинг-парогазовой фракции;
14. Абсорбционная насыпная колонна с отделением сбора легкого дистиллята;
15. Абсорбционная насыпная колонна с отделением сбора тяжелого дистиллята;
16. Абсорбционная насыпная колонна с отделением сбора крекинг дистиллята.
Принцип работы установки:
Установка работает как на твердом топливе, так и на жидком, с использованием универсальной газо-топливной горелки. Одна из причин экономичности использования установки - это ее возможность использования попутного не конденсируемого газа.
Пиролизная жидкость подается на секции тарелочного испарителя, которые соединены между собой последовательно, на разных уровнях. Каждая секция имеет разную определенную температуру нагрева, что позволяет производить ступенчатый нагрев сырья, выделяя фракции исходного нефтепродукта. После испарения в секциях выпаривателя парогазовая смесь поступает в блок конденсации, где она охлаждается и конденсируется в светлые нефтепродукты.
Показатели качества конечных товарных продуктов и материальный баланс привязан к исходному перерабатываемому сырью и зависит от его фракционного состава и температурных режимов дистилляции и крекинга установленных на контролерах регулирующей аппаратуры микро-НПЗ.
Производительность микро-НПЗ 500 - 1500 литров светлых нефтепродуктов в смену. Установленное напряжение 220V (По заказу можно исполнить питание всего электрооборудования от сети на 380V).
На микро-НПЗ основным сырьем работы блока нагрева для получения тепла используется перерабатываемое сырьё и попутный газ, образующийся при протекании процессов крекинга и дистилляции. Электропотребление оборудования минимально.
Микро-НПЗ содержит в себе возможность вести технологические процессы переработки жидкого углеводородного сырья одновременно в четырех режимах:
- режим дистилляции (температура 120-140°С)
- режим дистилляции (температура 260-280°С)
- режим дистилляции (температура 340-360°С)
- режим крекинга (температура 420-480°С) в остатке нефтяной кокс.
Качество светлых нефтепродуктов получаемых микро-НПЗ.
Бензин - прямогонный низкооктановый или бензин АИ-80 (ГОСТ) топливо для карбюраторных двигателей с искровым зажиганием. Отдельной перегонкой можно выделить легкий высокооктановый бензин в остатке будет тяжелый бензин. Для доведения до ГОСТа требует введения присадок или компаундирования с высокооктановыми бензинами.
Путем дополнительной разгонки и отбора фракций, выкипающих в определенных температурных пределах;
до 100°C — бензин I сорта,
до 130°C — бензин II сорта,
до 270°C — керосин обыкновенный.
Дизельное топливо - соответствует государственному стандарту: Топливо дизельное ГОСТ 305-82.
Получаемый при пиролизе полукокс.
Полученный при пиролизе полукокс предлагается подвергнуть дополнительной переработке сделав из него водо-угольное топливо (ВУТ) и использовать в хозяйстве как жидкое топливо (аналог дизельного) для водонагревателей системы отопления Потребителя
Суть предложения в следующем.
Полукокс, имея большую теплотворность, без переработки при применении в хозяйстве в качестве топлива имеет ряд существенных недостатков: сильно пылит, взрывоопасен, требует достаточно сложных технологических систем при его использовании в качестве топлива – систему хранения, подачи, выгрузки, транспортировки и т.д.
Для оптимизации использования полукокса предлагается его перерабатывать в водо-угольное топливо (ВУТ).
ВУТ представляет собой смесь тонкоизмельченного угля (или иного углеродосодержащего сырья в качестве добавки) с водой или водной эмульсией:
ВУТ = Уголь (58%...70%) + Водная эмульсия (29%…40%)
Как показывает технико-экономический анализ, добавка воды и её испарение в топке котла более эффективна, нежели предварительная сушка сырья, его помол, устранение взрывоопасности.
При использовании водных эмульсий мазутных смывов или эмульсий органического происхождения теплотворная способность ВУТ может быть дополнительно повышена.
Полученное таким способом ВУТ по своей вязкости близко к мазуту в нагретом состоянии, что позволяет перекачивать ВУТ насосами и использовать его для замены или дополнения угля, газа, мазута, дизеля.
Эксплуатационные характеристики
ВУТ обладает удобными эксплуатационными свойствами жидкого топлива, что необходимо для генерирующих станций от единиц до сотен мегаватт:
- Водоугольное топливо является не взрывоопасным, соответственно не требует повышенных мер по взрывоопасности.
- Водоугольное топливо воспламеняется только при температуре свыше 600 градусов. Соответственно, ВУТ является не пожароопасным.
- Удобно при перекачке, позволяет осуществлять постоянную дозированную подачу топлива (отсутствие “хлопков”).
- ВУТ применимо на большинстве водогрейныхых котлов в качестве основного либо дополнительного топлива.
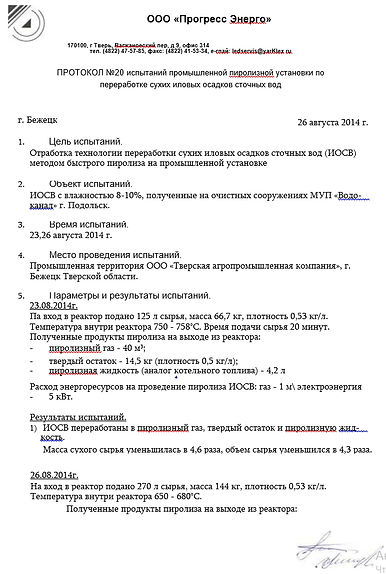
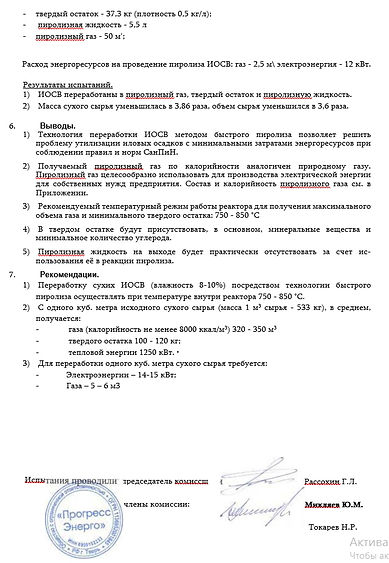
Инновационная технология плазменной газификации (выработка синтез-газа)
При данной технологии из энергоносителей образуется только газ.
Переработка осуществляется посредством использования плазмохимической технологии, которая является высокотемпературной разновидностью технологии пиролиза (газификации)
Технология проверена на мировых рынках, пригодна в дальнейшем для тиражирования
Ключевым преимуществом плазменной газификации в сравнении с обычной, используемой на сегодняшний день газификацией, является значительно более высокий температурный режим: до 5000 градусов, что делает технологию экологически чистой и практически безотходной.
Сравнительный анализ методов утилизации отходов
Технология переработки отходов
Подготовка сырья.
Происходит измельчение сырья, обезвоживание, доизмельчение и подача в плазменный реактор.
Необходимый температурный режим в реакторе обеспечивается работой плазмотрона, к которому непрерывно подводится электрический ток.
-
Плазменная или плазмохимическая технология переработки органических отходов является высокотемпературной разновидностью технологии пиролиза (газификации).
В реакционной камере осуществляется пиролизный процесс без доступа воздуха с образованием при высоких температурах (от 1300 до 2000°С) пиролизного газа, который дожигается в специальной камере. За счет энергии электрической дуги плазмотрона, пирогаз диссоциирует и ионизируется, превращаясь в плазму с высокой теплоемкостью и теплопроводностью.
Образовавшаяся в процессе деструкции газовая смесь поднимается в верхнюю часть реактора, отдает свое физическое тепло твердым отходам, за счет чего происходит их термодеструкция с образованием парогазовой смеси. Шлак, который накапливается в нижней части реактора в виде расплава, периодически удаляется.
-
Плазмообразующий газ продувается через электрическую дугу, где он ионизируется. Соединение основных атомов и молекул принимает форму синтез-газа, который используется для производства электричества и тепла, или как сырье для производства синтетических углеводородов. Полученное тепло используется в котле-утилизаторе для выработки пара и электроэнергии, а дымовые газы направляются на газоочистку.
-
Отходы подвергаются воздействию таких высоких температур, что органическая составляющая газифицируется и подвергается разделению на молекулы, а неорганическая составляющая образует стекловидный шлак. Отличия плазменного процесса от обычного сжигания отходов состоят в более высоких температурах и полностью замкнутом технологическом цикле системы. В плазменной системе образуется меньше твердых остатков, что упрощает их обработку.
-
Выходящий из реактора синтез-газ подвергается очистке от примесей, охлаждается до температур 250-400 градусов С
-
Синтез-газ направляется для выработки электроэнергии на газопоршневой электростанции
Часть произведенной электроэнергии отбирается для собственных нужд, в том числе для поддержания горения плазмотрона.
Стекловидный шлак может быть использован для производства газобетонов, теплоизоляционных плит и в качестве составной части дорожной одежды.
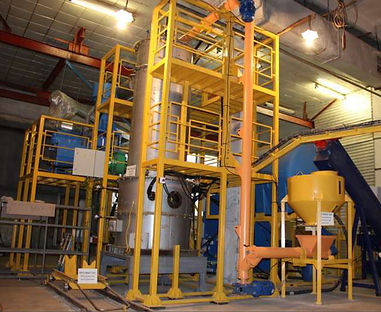

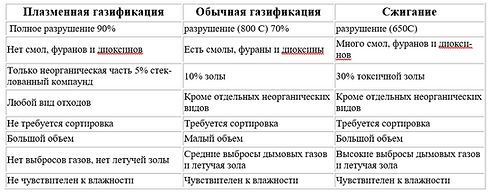




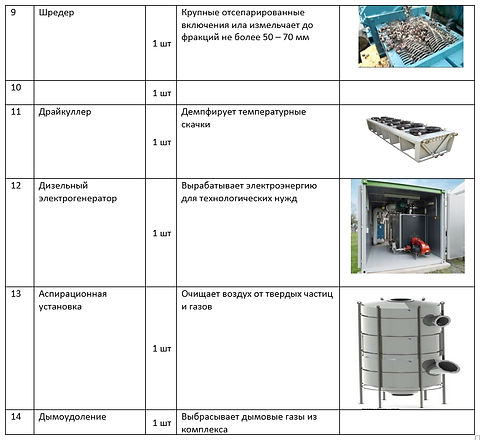
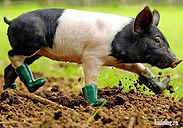

